3 Matic Software Free Download
Prepare your files for 3D Printing
- Materialise Magics
Data and Build preparation - Materialise Magics Essentials
Data preparation - Materialise MiniMagics
Free file viewer - Materialise e-Stage
Automatic support generation
Optimize your designs for 3D Printing
- Materialise 3-matic
Design optimization
Get the most out of your 3D printing machine
- Materialise Build Processor
Machine communication - Materialise Control Platform
Machine control and steering - Materialise Inspector
Process and Quality Control
Manage your AM production process
- Materialise Streamics
Production management
Solutions
Services
- Materialise Magics
Rapid Prototyping
- Technology Selector
Choose from a wide range of technologies - Material Selector
Choose a material and finish - Order Online
Get an instant quote on Materialise OnSite
Additive Manufacturing
- 3DPrintBarometer
Check for 3D printing suitability - Certified Additive Manufacturing
Turn your ideas into products - Cloud-Based 3D Printing Solutions
Streamline your 3D printing business
Design & Engineering
- Design for Additive Manufacturing
Benefit the most from 3D Printing - Remodeling & File Preparation
Get your data optimized - 3D Scanning & Measuring
Access customized metrology
Co-Creation
- 3DP Academy
Learn all about 3D Printing - Co-Creation Lab
Partner with our experts - 3DP Scan
Find 3D-printable parts
Solutions
- Full Service Metal AM
- Technology Selector
Materialise Mimics Care Suite
For Healthcare Professionals
Materialise Mimics Innovation Suite
For Engineers & Researchers
Solutions by Profession
Materialise Academy
A learning and knowledge exchange for clinicians, researchers and engineers
Software & Services
Resources
Company
Sustainability
People
Materialise 3-matic, a finite element analysis (FEA) mesh software for 3D analysis, anatomical. In an easy way with the Mimics Innovation Suite, brings you one step closer to a real clinical application. Download Materialise 3-matic 13.0.
Posted By Sculpteo on Aug 18, 2015 0 comments

How to optimize a mechanical design for 3D Printing? This topic is crucial when you’re re-designing an existing part, whose shape is derived from manufacturing needs. In this case study, we explain how to use cool softwares to re-design a part with the same function, same performance but less material.
2 weeks ago, Jess mentioned in an article about 3D Printing and mechanical engineering how we redesigned a spare part for an old ice-cream machine. This week, we would like to focus on the process of redesigning a part and the softwares you can use.
At Sculpteo we deal with ‘reverse engineering’ on a daily basis, this is one of the most common and appropriate applications for 3D printing: spare parts manufacturing.
In this case, the original component that this client provided us, in fact, belongs to a 30 year old ice-cream machine whose production has been stopped by the manufacturer, so it needed to be replaced due to wear and tear, our customer couldn’t rely on an original part any more and turned therefor to us. 3D Printing saved this client a lot of money compared to the option of acquiring a whole new machine.
After this first step we proposed to the client to redesign the part, optimizing it for additive manufacturing, which not only reduced its price, but also make it more efficient.
This room for improvement is due to the fact that the original part’s shape derives, apart from its function, from the manufacturing need of being extracted from a mold; this can be ignored since we are now using 3D Printing to produce it. Thanks to the “layer by layer” manufacturing process in fact, 3d Printing is able to give life to high complex shapes, with cavities and undercuts, otherwise impossible to produce with any other technology.
PowerProducer 6 - Create Stunning Blu-ray and DVD movie discs, the Easiest Way to Create Hollywood-Style Movie Discs. Cyberlink powerdirector 6 free download full version. Jan 30, 2018 - CyberLink PowerDirector 14 Ultimate incl Crack Full Version CyberLink PowerDirector 14 Ultimate: is an extreme video editing tool, pushing.
First Step: Stress Analysis
Our first goal was to define a new shape that would have allowed the piece to perform the same function, with same performances and durability, while considerably reducing the amount of material needed.
The time regulator goes haywire, hurtling various residents of different eras in time across time and space, and the gears that help the regulator function are scattered as well. - Bugs Bunny & Taz: Time Busters is a Looney Tunes platform video game released for the Sony PlayStation and Microsoft Windows in 2000, and is an indirect sequel to the 1999 game Bugs Bunny: Lost in Time. Daffy Duck accidentally breaks Granny's Time Regulator and is thrown back in time with the core of this machine, a precious Time Gem. Bugs bunny taz time busters no cd crack download. Bugs Bunny arrives at Granny's house, and is tasked with finding the Time Gem, the gears, the lost characters, and Daffy with Granny's pet Taz.
We got in touch with the client in order to understand how the part works inside the machine and interacts with other components; doing so we were able to apply loads, constraints and objectives to the digital model, relating them to the new material utilized: polyamide.
This process, called “stress analysis”, has a visual output that allows to understand how forces work across the part while performing the specific function. Thanks to this analysis we were able to design a new, more efficient, shape that was avoiding unnecessary material.
Software Free Download For Windows 7
We use solidThinking software for this first step. solidThinking Inspire is an efficient concept generation tool. Traditional structural simulations allow engineers to check if a design will support the required loads while solidThinking Inspire assists you by creating new geometry within your package space using the loads as an input (They offer a free trial).
This screenshot shows the part optimized after stress analysis.

2. Second step : Weight Reduction
Lastly we decided that we could reduce the weight of the part even more by applying a “lightweight” algorithm to the resulted model, transforming it in an even more intricate but still very resistant structure.
Professional solution to create this kind of structure are available (for instance 3-matic by Materialise) but the good news is that the free MeshMixer by Autodesk allows you also to apply this kind of volumetric patterns. We used the ‘make pattern’ tool to modify the 3D model.
Eventually we obtained a new optimized part, thanks to 3D printing.
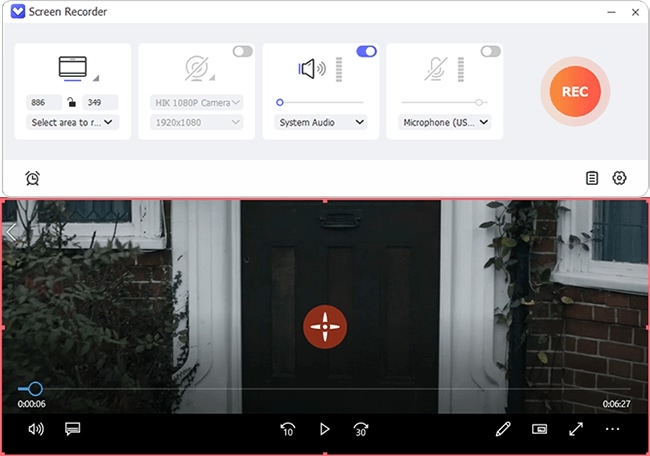
Taking structural benefits from 3D Printing into account is a difficult challenge when you’re designing. 3D softwares companies are working on reinventing the workflow. Autodesk’s Dreamcatcher project is for us a very promising. Here’s how they describe the project:
‘Project Dreamcatcher is an experimental design platform with focused research probes into generative design systems. The Dreamcatcher system allows designers to input specific design objectives, including functional requirements, material type, manufacturing method, performance criteria, and cost restrictions. Loaded with design requirements, the system then searches a procedurally synthesized design space to evaluate a vast number of generated designs for satisfying the design requirements. The resulting design alternatives are then presented back to the user, along with the performance data of each solution, in the context of the entire design solution space. (…)
After a number of solutions have been computationally generated from a problem definition, the Dreamcatcher design explorer presents to the user a set of possible solutions and their associated solution strategies. This user interface provides a sense of the shape of the valid design space and variable interactions. It also assists users in building a mental model of which alternatives are high performing relative to all others in the set. Once the solution has been adequately explored, the designer can modify the problem definition to iteratively generate more relevant solutions.’
If you’re redesigning a part, and thinking of lightweight structure, don’t hesitate to contact us and share, we would be happy to help!